The “Industrial Printing” research group deals with a wide range of topics related to printing. All of them have the goal of automating the printing process and the various pre- and post-treatment steps and increasing the quality and productivity achieved. In addition, there is a strong focus on the technology transfer of our findings into applications.
IDD's laboratory equipment is divided into several labs. The 3D printing labs include several printers using filament based, stereolithography and selective laser sintering techniques, as well as a wide variety of 3D scanners. The printers are optimized for various special applications such as printing high-performance polymers, printing with multiple materials and printing of biomaterials, the use of special extruders, etc. The conventional printing lab has a three-level setup from printability devices with lowest substrate and fluid consumption to lab printing machines and finally to industrial production machines. All common printing processes such as offset, gravure, screen, flexo and inkjet printing as well as embossing processes are available. In the area of pre-treatment as well as post-treatment, a wide variety of equipment such as corona and plasma systems as well as UV, IR, flash and hot air dryers and laser post-treatment are available for 3D as well as conventional printing processes.
We operate a climate control laboratory that controls humidity and temperature to the highest accuracy levels, as well as reducing particle contamination in the room. Here, mainly mechanical material characterization can be performed with procedures according to standards and special setups, but also printing can be performed under controlled climatic conditions. In the characterization laboratory, polymers, fluids, substrates and printed products can be examined using optical microscopic, profilometric, mechanical, electrical and rheological measurement techniques.
To achieve the goals mentioned at the beginning, the materials involved in the printing process are investigated, the sub-processes are modeled and simulated and, in the end, a targeted further development of the overall printing process is achived.
The materials and process steps involved are examined and characterized close to production using highly specialized measuring equipment and sensors or individually developed test rigs. Hardware from National Instruments and the corresponding software package LabView are mostly used for this purpose. DoE (Design of Experiments) tools are used for experiment design, and the analysis of large amounts of data (Big Data) may be necessary for evaluation. On the basis of the measurement data and the correlations determined in the process, modeling and simulation of sub-processes and components is carried out in order to achive a targeted improvement of the overall process. Ansys and Abaqus in particular, but also open source solutions such as Salome-Meca and Code-Aster, are used for this purpose, which is of particular interest to small and medium-sized companies. With regard to industrial process control, measurement technology for monitoring or controls for machines are designed, test setups are developed or new machine parts are designed in order to be able to realize new types of printing and manufacturing opportunities.
Currently, our methods for advanced printing applications are used in several projects, mainly in the field of 3D printing and here especially for fused filament fabrication and vat-based stereolithography. Here, the limits of known 3D printing methods are challenged, new manufacturing methods are developed and, above all, manufacturing processes are established for parts that could not previously be realized using printing methods. In addition, conventional printing processes are also being investigated for various applications such as security features and graphic effects.
Another area of development is the automation and application of artificial intelligence and machine learning methods for Industry 4.0, from data-driven design of printing components such as printing pads to sensor data fusion to generate training models for AI-based process controls.
In addition, technology transfer is taking up more and more space and resulted in business model developments, participations in spin-offs and start-ups or rights transfers in a wide variety of topics such as special purpose machinery manufacture, 3D printing and diagnostic applications.
The long-term visions are the establishment of the following topics
- 4D printing: Here, graphic as well as technical coatings on 3-dimensional objects are of great interest. We have already worked on these topics in several projects and want to specialize in this area in the long term.
- Electrical functions in 3D-printed components: Here we can develop specialized solutions in cooperation with the other research groups of the institute, especially in the field of automotive industry and medical technology, for example to integrate sensors in 3D-printed implants.
- Product integration: As in the previously mentioned example of sensors in 3D-printed implants, the keyword product integration is a strongly developing topic area for highly specialized solutions, for which many of our previous projects already provide examples. We want to intensify this further in order to be able to apply our knowledge here in a targeted manner.
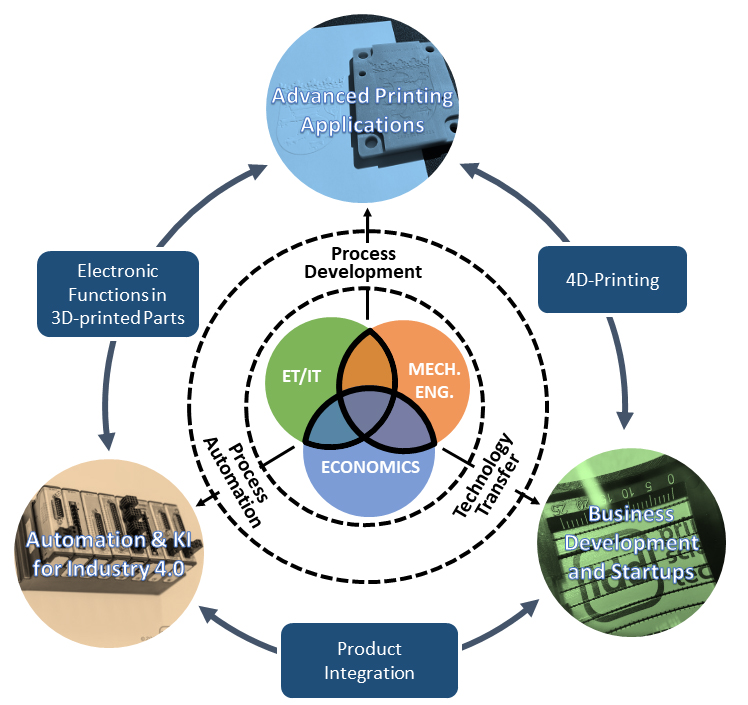
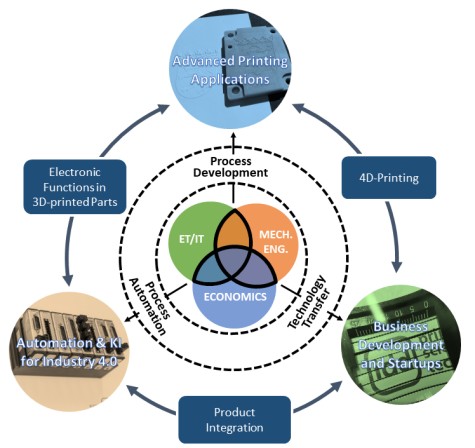